Optimizing your warehouse operations can lead to increased efficiency, reduced costs, and improved customer satisfaction. With advancements in technology and strategic planning, today’s warehouses can operate at unprecedented levels of sophistication. Training for employees, leveraging cutting-edge technologies, implementing robust warehouse management systems, and adopting lean practices are among the cornerstones for achieving operational excellence. Keep reading to discover how these resources can transform your warehouse into a model of efficiency.
Warehouse Management Systems (WMS): Streamlining Inventory and Processes
Warehouse management software (WMS) stands at the core of modern warehousing, serving as the central point for operations, data collection, and process optimization. These systems offer comprehensive functionalities that go beyond simple inventory management. They coordinate various aspects of supply chain logistics, including receiving, put-away, inventory control, order fulfillment, and shipping.
One of the key benefits of a WMS is its ability to provide real-time visibility into inventory levels and location within the warehouse. This transparency not only prevents overstocking or stockouts but also enables faster response times to customer orders. Up-to-the-minute data is vital for businesses to remain competitive in an on-demand marketplace.
Moreover, a WMS can integrate seamlessly with other systems, such as transportation management and WMS, creating a unified solution for process efficiency. The automation of repetitive tasks eliminates manual data entry, reduces errors, and frees up staff to focus on more complex, value-added tasks. A good WMS empowers warehouses to scale operations and adapt to changing business needs with agility.
Essential Training for Warehouse Staff to Enhance Productivity
In the world of warehousing, a well-trained staff is a crucial component of seamless operations. Ensuring that all team members are proficient in the handling of technology and equipment not only boosts productivity but also minimizes the risk of accidents. Continuous education and training programs help in retaining valuable employees by fostering a culture of growth and development.
Leadership training is equally important, as skilled managers and supervisors play a pivotal role in implementing new technologies and procedures. By equipping them with the right tools and knowledge, they can effectively lead their teams, optimize workflow, and sustain high performance. Effective communication skills, problem-solving abilities, and strategic thinking are among the training focal points for leadership roles.
It’s also crucial to provide operational training which includes best practices for picking, packing, and shipping. Customized training programs can be developed based on the specific needs of a warehouse and its workforce, allowing for flexibility in teaching methods and modalities. This might include hands-on training, simulations, and e-learning modules, ensuring that staff are prepared for the diverse challenges they face daily.
The Role of Automation and Robotics in Modern Warehousing
The introduction of automation and robotics in the warehousing sector has revolutionized how goods are stored, handled, and transported. Automated guided vehicles (AGVs) and robotic picking systems are increasingly common, providing accurate and speedy movement of items within the warehouse. The adoption of these automated systems leads to reduced labor costs and human error, as well as increased throughput.
Robotics has also brought about a new level of precision in tasks that are repetitive or physically demanding. Robotic arms can be programmed to sort, pack, and palletize products with consistent speed and accuracy. This technological shift not only improves efficiency but also addresses workforce challenges by reducing the need for manual labor in tasks susceptible to injuries and fatigue.
Implementing Lean Practices to Reduce Waste and Improve Operations
Lean practices, which originated in manufacturing, have been adapted to warehouse operations to minimize waste and maximize value. The core principle is to streamline processes by eliminating non-value-adding steps, thus improving efficiency and cutting costs. Lean warehousing targets several types of waste, including excess inventory, overproduction, and unnecessary motion or transportation of goods.
One aspect of lean warehousing is the organization and cleanliness of the facility itself. Through the 5S methodology: sort, set in order, shine, standardize, and sustain warehouses can maintain an orderly environment that promotes safety and reduces time spent searching for items. This systemic approach improves workflow and reduces downtime, thus increasing productivity.
Altogether, warehouses that harness innovative technologies, invest in staff training, implement advanced management systems, and adopt lean practices are well-equipped to meet the demands of the modern economy. These resources pave the way for a new era of warehousing, characterized by agility, efficiency, and continuous improvement. Overall, a commitment to these strategies is essential for any business looking to optimize its warehousing operations.
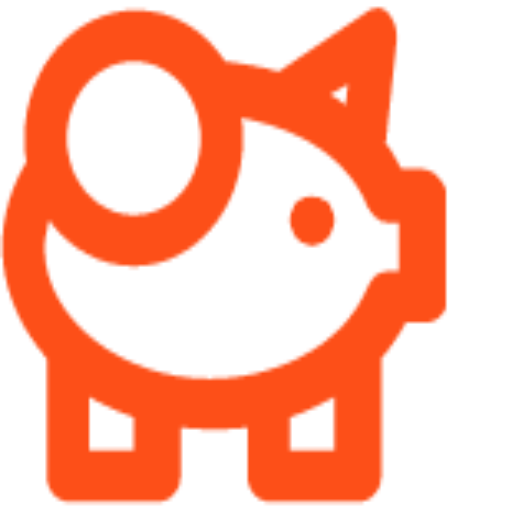
MoneyMantra, is a passionate content creator with over 5 years of experience in writing about the intersection of technology, business, finance, education, and more. With a deep understanding of how these fields empower both individuals and businesses